Our Services
At MicroType Engineering, we bridge the gap between your ideas and fully realized products. Whether you have a concept in its earliest stages or need support refining a working prototype, we bring the expertise, tools, and innovation required to complement your team’s capabilities.
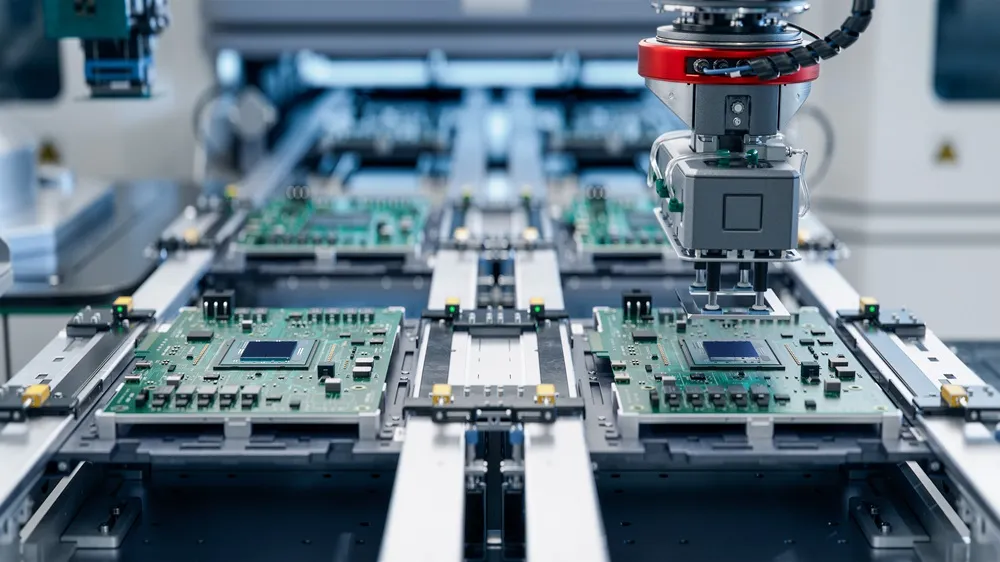
Our Comprehensive Services
PCB Design
We specialize in designing high-performance printed circuit boards tailored to your product requirements. From schematics to layout, we ensure precision, functionality, and manufacturability.
Industrial & Mechanical Design
We create robust and efficient mechanical designs that integrate seamlessly with electronic systems. Our designs focus on functionality, durability, and aesthetics to align with your project goals.
Software Development
Our team develops custom software solutions to power your devices and systems, ensuring they perform reliably and meet your specific application needs.
Firmware Development
From embedded systems to device-level firmware, we write efficient and optimized code that allows your hardware to operate seamlessly and effectively.
Test Planning
We develop comprehensive testing plans to verify your product’s performance, functionality, and reliability, ensuring any issues are identified and addressed early.
Prototyping
We bring your ideas to life with fully functional prototypes, allowing you to test, iterate, and validate designs before moving into full-scale production.
Design for Manufacturability
Our DFM services ensure your design is optimized for efficient production, reducing costs and streamlining the manufacturing process.
Quality Assurance (QA)
We implement rigorous QA processes to verify that your product meets quality standards, from initial concept to production-ready prototypes.
PCB Production
We handle small and large-scale PCB production with precision and efficiency, delivering high-quality boards that meet your specifications and deadlines.
CNC Fabrication
Our CNC fabrication services provide precision machining for custom components, ensuring high tolerances and exact fits for your project.
Box Builds
We provide complete box build solutions, including system integration, enclosure assembly, wiring, and final testing, delivering ready-to-use products.
EMC Pre-Compliance Testing
We conduct pre-compliance EMC testing to help you identify and resolve potential electromagnetic compatibility issues, ensuring your product meets industry standards.
Unit Testing
We develop and perform thorough unit tests to validate individual components, ensuring your product operates reliably at every level.
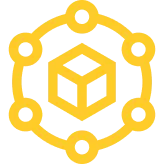
Supply Chain Management
From sourcing components to coordinating production, our supply chain management services ensure your project stays on time, on budget, and fully optimized for success.
Partner With Us
Partner with a team that combines creative engineering and rigorous compliance. Operating under AS9100 and ITAR, MicroType Engineering delivers traceable quality for defense and commercial projects alike. From initial sketch to final build, we provide the discipline, transparency and speed needed to bring your innovation to market with the confidence your customers demand.